ସେଠାରେ ଅନେକ ପ୍ରକାରର ଫିଡ୍ ପ୍ରକ୍ରିୟାକରଣ ଉପକରଣ ଅଛି, ଯେଉଁଥିରେ ମୁଖ୍ୟ ଉପକରଣ ଯାହା ଫିଡ୍ ଗ୍ରାନୁଲେସନ୍ ଉପରେ ପ୍ରଭାବ ପକାଇଥାଏ, ତାହା ହାମର ମିଲ୍, ମିକ୍ସର୍ସ ଏବଂ ପେଲେଟ୍ ମେସିନ୍ ଛଡା ଆଉ କିଛି ନୁହେଁ |ଆଜିର କ୍ରମାଗତ ପ୍ରତିଯୋଗିତାରେ, ଅନେକ ଉତ୍ପାଦକ ଉନ୍ନତ ଉତ୍ପାଦନ ଉପକରଣ କ୍ରୟ କରନ୍ତି, କିନ୍ତୁ ଭୁଲ କାର୍ଯ୍ୟ ଏବଂ ବ୍ୟବହାର ହେତୁ ଯନ୍ତ୍ରପାତି ବିଫଳତା ପ୍ରାୟତ। ଘଟେ |ତେଣୁ, ଫିଡ୍ ଉତ୍ପାଦନକାରୀଙ୍କ ଦ୍ୱାରା ଉପକରଣ ବ୍ୟବହାର ସତର୍କତାର ସଠିକ୍ ବୁ understanding ାମଣାକୁ ଅଣଦେଖା କରାଯାଇପାରିବ ନାହିଁ |
1. ହାମର୍ ମିଲ୍ |
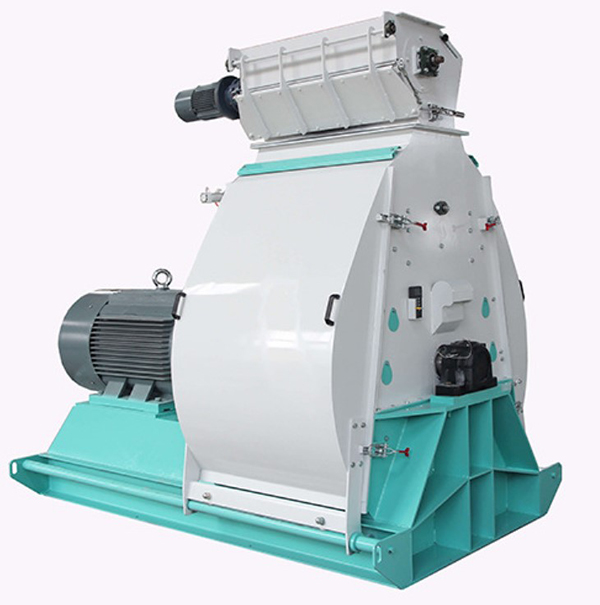
ହାମର ମିଲର ସାଧାରଣତ two ଦୁଇଟି ପ୍ରକାର ଥାଏ: ଭୂଲମ୍ବ ଏବଂ ଭୂସମାନ୍ତର |ହାମର ମିଲର ମୁଖ୍ୟ ଉପାଦାନଗୁଡ଼ିକ ହେଉଛି ହାତୁଡ଼ି ଏବଂ ସ୍କ୍ରିନ୍ ବ୍ଲେଡ୍ |ହାତୁଡ଼ି ବ୍ଲେଡଗୁଡିକ ସ୍ଥାୟୀ, ପରିଧାନ-ପ୍ରତିରୋଧୀ ହେବା ଉଚିତ ଏବଂ ଯନ୍ତ୍ରର କମ୍ପନ ସୃଷ୍ଟି ନକରିବା ପାଇଁ ଏକ ସନ୍ତୁଳିତ manner ଙ୍ଗରେ ବ୍ୟବହୃତ ହେବା ଉଚିତ୍ |
ହାତୁଡ଼ି ମିଲ ବ୍ୟବହାର ପାଇଁ ସତର୍କତା:
1) ମେସିନ୍ ଆରମ୍ଭ କରିବା ପୂର୍ବରୁ, ସମସ୍ତ ସଂଯୋଗକାରୀ ଅଂଶ ଏବଂ ବିୟରିଂର ତେଲ ଲଗାନ୍ତୁ |ମେସିନ୍ କୁ 2-3 ମିନିଟ୍ ପାଇଁ ଖାଲି ଚଲାନ୍ତୁ, ସାଧାରଣ କାର୍ଯ୍ୟ ପରେ ଖାଇବା ଆରମ୍ଭ କରନ୍ତୁ, କାମ ସରିବା ପରେ ଖାଇବା ବନ୍ଦ କରନ୍ତୁ ଏବଂ ମେସିନ୍ କୁ 2-3 ମିନିଟ୍ ପାଇଁ ଖାଲି ଚଲାନ୍ତୁ |ମେସିନ୍ ଭିତରେ ଥିବା ସମସ୍ତ ସାମଗ୍ରୀ ନିଷ୍କାସିତ ହେବା ପରେ ମୋଟରକୁ ବନ୍ଦ କର |
)) ହାତୁଡ଼ିକୁ ତୁରନ୍ତ ବୁଲାଇ ସେଣ୍ଟଲାଇନ୍ ପିନ୍ଧିବା ସମୟରେ ବ୍ୟବହାର କରାଯିବା ଉଚିତ୍ |ଯଦି ସମସ୍ତ ଚାରି କୋଣକୁ କେନ୍ଦ୍ରରେ ପିନ୍ଧାଯାଏ, ତେବେ ଏକ ନୂତନ ହାତୁଡ଼ି ପ୍ଲେଟ୍ ବଦଳାଇବା ଆବଶ୍ୟକ |ଧ୍ୟାନ: ବଦଳାଇବା ସମୟରେ, ମୂଳ ବ୍ୟବସ୍ଥା କ୍ରମକୁ ପରିବର୍ତ୍ତନ କରାଯିବା ଉଚିତ୍ ନୁହେଁ, ଏବଂ ହାମର ଖଣ୍ଡଗୁଡିକର ପ୍ରତ୍ୟେକ ଗୋଷ୍ଠୀ ମଧ୍ୟରେ ଓଜନ ପାର୍ଥକ୍ୟ 5g ରୁ ଅଧିକ ହେବା ଉଚିତ୍ ନୁହେଁ, ନଚେତ୍ ଏହା ରୋଟରର ସନ୍ତୁଳନକୁ ପ୍ରଭାବିତ କରିବ |
)) କ୍ରାସ୍ ଦକ୍ଷତା ବୃଦ୍ଧି ଏବଂ ଧୂଳି ହ୍ରାସ କରିବା ପାଇଁ ହାମର ମିଲର ଏୟାର ନେଟୱାର୍କ ସିଷ୍ଟମ ଗୁରୁତ୍ୱପୂର୍ଣ୍ଣ, ଏବଂ ଭଲ କାର୍ଯ୍ୟଦକ୍ଷତା ସହିତ ନାଡ ଧୂଳି ସଂଗ୍ରହକାରୀ ସହିତ ମେଳ ହେବା ଉଚିତ |ପ୍ରତ୍ୟେକ ସିଫ୍ଟ ପରେ ଧୂଳି ସଂଗ୍ରହକାରୀର ଭିତର ଓ ବାହାରେ ସଫା କର ଏବଂ ଧୂଳି କା remove ିବା ପାଇଁ ନିୟମିତ ଭାବରେ ଯାଞ୍ଚ, ସଫା ଏବଂ ତେଲ ଲଗାନ୍ତୁ |
4) ସାମଗ୍ରୀଗୁଡିକ ଲୁହା ବ୍ଲକ୍, ଚୂର୍ଣ୍ଣ ପଥର ଏବଂ ଅନ୍ୟାନ୍ୟ ଆବର୍ଜନା ସହିତ ମିଶ୍ରିତ ହେବା ଉଚିତ୍ ନୁହେଁ |କାର୍ଯ୍ୟ ପ୍ରକ୍ରିୟା ସମୟରେ ଯଦି ଅସ୍ୱାଭାବିକ ଶବ୍ଦ ଶୁଣାଯାଏ, ଯାଞ୍ଚ ଏବଂ ତ୍ରୁଟି ନିବାରଣ ପାଇଁ ଯନ୍ତ୍ରକୁ ଠିକ୍ ସମୟରେ ବନ୍ଦ କରନ୍ତୁ |
5) ହାମର ମିଲର ଉପର ମୁଣ୍ଡରେ ଥିବା ଫିଡରର କାର୍ଯ୍ୟକ୍ଷମ କରେଣ୍ଟ ଏବଂ ଫିଡିଂ ପରିମାଣ ବିଭିନ୍ନ ସାମଗ୍ରୀ ଅନୁଯାୟୀ ଯେକ time ଣସି ସମୟରେ ଆଡଜଷ୍ଟ ହେବା ଉଚିତ ଏବଂ ଜାମକୁ ରୋକିବା ଏବଂ ଚୂର୍ଣ୍ଣ ପରିମାଣ ବୃଦ୍ଧି କରିବା |
2. ମିକ୍ସର୍ (ପ୍ୟାଡଲ୍ ମିକ୍ସର୍ କୁ ଏକ ଉଦାହରଣ ଭାବରେ ବ୍ୟବହାର କରି)
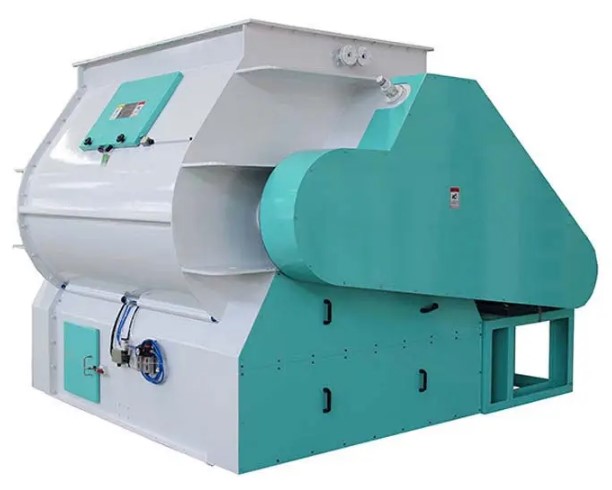
ଡୁଆଲ୍ ଅକ୍ସ ପ୍ୟାଡଲ୍ ମିକ୍ସର୍ ଏକ କେସିଙ୍ଗ୍, ରୋଟର୍, କଭର, ଡିସଚାର୍ଜ structure ାଞ୍ଚା, ଟ୍ରାନ୍ସମିସନ୍ ଡିଭାଇସ୍ ଇତ୍ୟାଦିରେ ଗଠିତ | ବିପରୀତ ଘୂର୍ଣ୍ଣନ ଦିଗ ସହିତ ମେସିନରେ ଦୁଇଟି ରୋଟର୍ ଅଛି |ରୋଟର୍ ମୁଖ୍ୟ ଶାଫ୍ଟ, ବ୍ଲେଡ୍ ଶାଫ୍ଟ ଏବଂ ବ୍ଲେଡ୍ ଦ୍ୱାରା ଗଠିତ |ବ୍ଲେଡ୍ ଶାଫ୍ଟ ମୁଖ୍ୟ ଶାଫ୍ଟ କ୍ରସ୍ ସହିତ ବିଚ୍ଛେଦ ହୁଏ, ଏବଂ ବ୍ଲେଡ୍ ଏକ ସ୍ୱତନ୍ତ୍ର କୋଣରେ ବ୍ଲେଡ୍ ଶାଫ୍ଟରେ eld ାଲାଯାଏ |ଗୋଟିଏ ପଟେ, ପଶୁ ସାମଗ୍ରୀ ସହିତ ବ୍ଲେଡ୍ ମେସିନ୍ ସ୍ଲଟ୍ ର ଭିତର କାନ୍ଥରେ ଘୂର୍ଣ୍ଣନ କରେ ଏବଂ ଅନ୍ୟ ପ୍ରାନ୍ତ ଆଡକୁ ଗତି କରେ, ଯାହା ଦ୍ animal ାରା ପଶୁ ସାମଗ୍ରୀ ପରସ୍ପର ସହିତ ଫ୍ଲିପ୍ ହୋଇଯାଏ ଏବଂ ଦ୍ରୁତ ଏବଂ ସମାନ ମିଶ୍ରଣ ପ୍ରଭାବ ହାସଲ କରେ |
ମିକ୍ସର୍ ବ୍ୟବହାର ପାଇଁ ସତର୍କତା:
1) ମୁଖ୍ୟ ଶାଫ୍ଟ ସାଧାରଣ ଭାବରେ ଘୂର୍ଣ୍ଣନ କରିବା ପରେ, ପଦାର୍ଥ ଯୋଗ କରାଯିବା ଉଚିତ |ମୂଖ୍ୟ ପଦାର୍ଥର ଅଧା ବ୍ୟାଚ୍ ଭିତରକୁ ପ୍ରବେଶ କରିବା ପରେ ଯୋଗୀଗୁଡିକ ଯୋଗ କରାଯିବା ଉଚିତ ଏବଂ ସମସ୍ତ ଶୁଖିଲା ସାମଗ୍ରୀ ଯନ୍ତ୍ରରେ ପ୍ରବେଶ କରିବା ପରେ ଗ୍ରୀସ୍ ସ୍ପ୍ରେ କରାଯିବା ଉଚିତ୍ |କିଛି ସମୟ ପାଇଁ ସ୍ପ୍ରେ ଏବଂ ମିଶ୍ରଣ ପରେ, ପଦାର୍ଥ ଡିସଚାର୍ଜ ହୋଇପାରେ;
2) ଯେତେବେଳେ ମେସିନ୍ ବନ୍ଦ ହୋଇଯାଏ ଏବଂ ବ୍ୟବହାରରେ ନଥାଏ, କଠିନ ହେବା ପରେ ପାଇପଲାଇନକୁ ବନ୍ଦ ନକରିବା ପାଇଁ ଗ୍ରୀସ୍ ଯୋଗ କରୁଥିବା ପାଇପ୍ ଲାଇନରେ କ gre ଣସି ଗ୍ରୀସ୍ ରଖିବା ଉଚିତ୍ ନୁହେଁ |
)) ସାମଗ୍ରୀ ମିଶ୍ରଣ କରିବା ସମୟରେ, ଧାତୁ ଅପରିଷ୍କାରଗୁଡିକ ମିଶ୍ରିତ ହେବା ଉଚିତ୍ ନୁହେଁ, କାରଣ ଏହା ରୋଟର୍ ବ୍ଲେଡ୍ ନଷ୍ଟ କରିପାରେ |
4) ବ୍ୟବହାର ସମୟରେ ଯଦି ଏକ ବନ୍ଦ ହୋଇଯାଏ, ମୋଟର ଆରମ୍ଭ କରିବା ପୂର୍ବରୁ ମେସିନ୍ ଭିତରେ ଥିବା ପଦାର୍ଥକୁ ଡିସଚାର୍ଜ କରାଯିବା ଉଚିତ୍;
5) ଯଦି ଡିସଚାର୍ଜ କବାଟରୁ କ le ଣସି ଲିକ୍ ଥାଏ, ତେବେ ଡିସଚାର୍ଜ କବାଟ ଏବଂ ମେସିନ୍ କେସିଙ୍ଗର ସିଲ୍ ସିଟ୍ ମଧ୍ୟରେ ସମ୍ପର୍କ ଯାଞ୍ଚ କରାଯିବା ଉଚିତ, ଯେପରି ଡିସଚାର୍ଜ କବାଟ ବନ୍ଦ ହୋଇନଥାଏ;ଟ୍ରାଭେଲ୍ ସୁଇଚ୍ ର ସ୍ଥିତିକୁ ସଜାଡିବା ଉଚିତ୍, ବାସ୍ତୁ ଦ୍ୱାରର ତଳ ଭାଗରେ ଥିବା ବାଦାମକୁ ସଜାଡିବା ଉଚିତ୍, କିମ୍ବା ସିଲ୍ ଷ୍ଟ୍ରିପ୍ ବଦଳାଇବା ଉଚିତ |
3. ରିଙ୍ଗ୍ ଡାଏ ପେଲେଟ୍ ମେସିନ୍ |
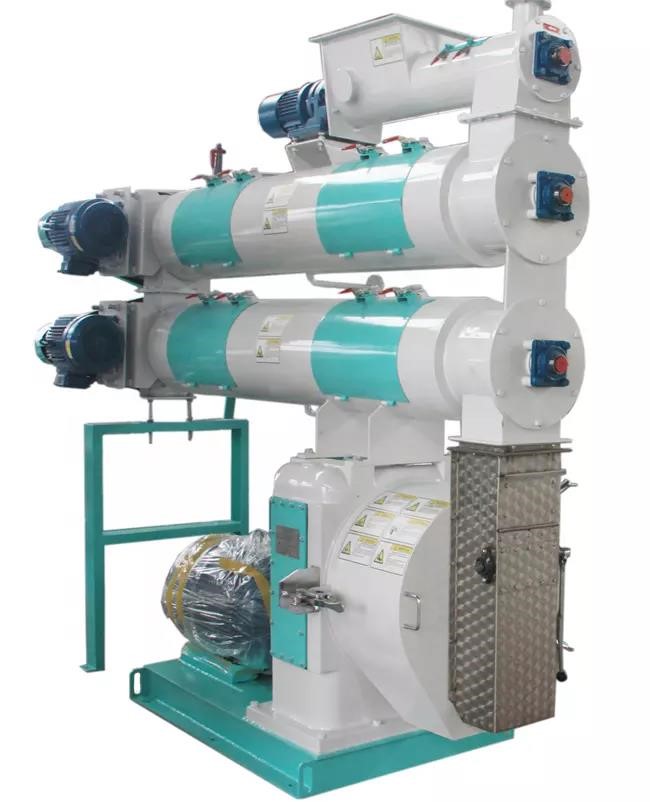
ବିଭିନ୍ନ ଫିଡ୍ କାରଖାନାର ଉତ୍ପାଦନ ପ୍ରକ୍ରିୟାରେ ପେଲେଟ୍ ମେସିନ୍ ହେଉଛି ଏକ ପ୍ରମୁଖ ଉପକରଣ, ଏବଂ ଏହାକୁ ଫିଡ୍ କାରଖାନାର ହୃଦୟ ବୋଲି ମଧ୍ୟ କୁହାଯାଇପାରେ |ପେଲେଟ ମେସିନର ସଠିକ୍ ବ୍ୟବହାର ସିଧାସଳଖ ଉତ୍ପାଦର ଗୁଣବତ୍ତା ଉପରେ ପ୍ରଭାବ ପକାଇଥାଏ |
ପେଲେଟ ମେସିନ୍ ବ୍ୟବହାର ପାଇଁ ସତର୍କତା:
1) ଉତ୍ପାଦନ ପ୍ରକ୍ରିୟା ସମୟରେ, ଯେତେବେଳେ ଅତ୍ୟଧିକ ସାମଗ୍ରୀ ପେଲେଟ୍ ମେସିନ୍ରେ ପ୍ରବେଶ କରେ, ଯାହା ହଠାତ୍ କରେଣ୍ଟରେ ବୃଦ୍ଧି ଘଟାଏ, ବାହ୍ୟ ନିଷ୍କାସନ ପାଇଁ ଏକ ମାନୁଆଲ୍ ଡିସଚାର୍ଜ ପ୍ରଣାଳୀ ବ୍ୟବହାର କରାଯିବା ଆବଶ୍ୟକ |
)) ପେଲେଟ ମେସିନର କବାଟ ଖୋଲିବାବେଳେ ପ୍ରଥମେ ବିଦ୍ୟୁତ କାଟ ହେବା ଆବଶ୍ୟକ, ଏବଂ ପେଲେଟ ମେସିନ୍ ଚାଲିବା ବନ୍ଦ ହେବା ପରେ ହିଁ କବାଟ ଖୋଲାଯାଇପାରିବ |
3) ପେଲେଟ୍ ମେସିନ୍ ପୁନ rest ଆରମ୍ଭ କରିବାବେଳେ, ପେଲେଟ୍ ମେସିନ୍ ଆରମ୍ଭ କରିବା ପୂର୍ବରୁ ପେଲେଟ୍ ମେସିନ୍ ରିଙ୍ଗ୍ ଡାଏ (ଗୋଟିଏ ଟର୍ନ୍) କୁ ମାନୁଆଲ ଭାବରେ ଘୂର୍ଣ୍ଣନ କରିବା ଆବଶ୍ୟକ |
4) ଯେତେବେଳେ ମେସିନ୍ ତ୍ରୁଟିପୂର୍ଣ୍ଣ ହୁଏ, ବିଦ୍ୟୁତ୍ ଯୋଗାଣ ବନ୍ଦ ହେବା ଆବଶ୍ୟକ ଏବଂ ତ୍ରୁଟି ନିବାରଣ ପାଇଁ ମେସିନ୍ ବନ୍ଦ ହେବା ଜରୁରୀ |କାର୍ଯ୍ୟ ସମୟରେ କଠିନ ତ୍ରୁଟି ନିବାରଣ ପାଇଁ ହାତ, ପାଦ, କାଠ ବାଡ଼ି, କିମ୍ବା ଲୁହା ଉପକରଣ ବ୍ୟବହାର କରିବା ନିଷେଧ;ବଳପୂର୍ବକ ମୋଟର ଆରମ୍ଭ କରିବା ନିଷେଧ |
5) ପ୍ରଥମ ଥର ପାଇଁ ଏକ ନୂଆ ରିଙ୍ଗ୍ ମରିବାବେଳେ ଏକ ନୂତନ ପ୍ରେସର ରୋଲର୍ ବ୍ୟବହାର କରାଯିବା ଆବଶ୍ୟକ |ତେଲକୁ ସୂକ୍ଷ୍ମ ବାଲି ସହିତ ମିଶ୍ରଣ କରାଯାଇପାରେ (ସମସ୍ତ ଏକ 40-20 ଜାଲ୍ ସି ieve ି ଦେଇ ପଦାର୍ଥର ଅନୁପାତ ସହିତ: ତେଲ: ବାଲି ପ୍ରାୟ 6: 2: 1 କିମ୍ବା 6: 1: 1) ରିଙ୍ଗକୁ ଧୋଇବା ପାଇଁ 10 ରୁ 20 ପର୍ଯ୍ୟନ୍ତ ମରାଯାଏ | ମିନିଟ୍, ଏବଂ ଏହାକୁ ସାଧାରଣ ଉତ୍ପାଦନରେ ରଖାଯାଇପାରିବ |
6) ରକ୍ଷଣାବେକ୍ଷଣ ଶ୍ରମିକମାନଙ୍କୁ ବର୍ଷକୁ ଥରେ ମୁଖ୍ୟ ମୋଟର ବିୟରିଂ ଯାଞ୍ଚ ଏବଂ ଇନ୍ଧନ ଦେବାରେ ସାହାଯ୍ୟ କରନ୍ତୁ |
7) ପେଲେଟ ମେସିନର ଗିଅରବକ୍ସ ପାଇଁ ବର୍ଷକୁ 1-2 ଥର ଲବ୍ରିକେଟ୍ ତେଲ ବଦଳାଇବାରେ ରକ୍ଷଣାବେକ୍ଷଣ କର୍ମଚାରୀମାନଙ୍କୁ ସାହାଯ୍ୟ କରନ୍ତୁ |
8) ସ୍ଥାୟୀ ଚୁମ୍ବକୀୟ ସିଲିଣ୍ଡରକୁ ପ୍ରତି ସିଫ୍ଟରେ ଅତି କମରେ ଥରେ ସଫା କରନ୍ତୁ |
9) କଣ୍ଡିସନର ଜ୍ୟାକେଟରେ ପ୍ରବେଶ କରୁଥିବା ବାଷ୍ପ ଚାପ 1kgf / cm2 ରୁ ଅଧିକ ହେବ ନାହିଁ |
10) କଣ୍ଡିସନରରେ ପ୍ରବେଶ କରୁଥିବା ବାଷ୍ପ ଚାପ ପରିସର ହେଉଛି 2-4kgf / cm2 (ସାଧାରଣତ 2.5 2.5 kgf / cm2 ରୁ କମ୍ ନୁହେଁ) |
11) ପ୍ରେସର ରୋଲରକୁ ପ୍ରତି ସିଫ୍ଟରେ 2-3 ଥର ତେଲ ଦିଅନ୍ତୁ |
12) ସପ୍ତାହରେ 2-4 ଥର ଫିଡର୍ ଏବଂ କଣ୍ଡିସନରକୁ ସଫା କରନ୍ତୁ (ଦିନରେ ଦିନରେ ଥରେ) |
13) କଟି ଛୁରୀ ଏବଂ ରିଙ୍ଗ ମର ମଧ୍ୟରେ ଦୂରତା ସାଧାରଣତ 3 3 ମିମିରୁ କମ୍ ନୁହେଁ |
14) ସାଧାରଣ ଉତ୍ପାଦନ ସମୟରେ, ଯେତେବେଳେ ଏହାର କରେଣ୍ଟ୍ ରେଟେଡ୍ କରେଣ୍ଟକୁ ଅତିକ୍ରମ କରେ, ସେତେବେଳେ ମୁଖ୍ୟ ମୋଟରକୁ ଓଭରଲୋଡ୍ କରିବାକୁ କଠୋର ନିଷେଧ |
ଯାନ୍ତ୍ରିକ ସହାୟତା ଯୋଗାଯୋଗ ସୂଚନା |ବ୍ରୁସ୍
TEL / ହ୍ ats ାଟସ୍ ଆପ୍ / ୱେଚ୍ / ଲାଇନ: +86 18912316448 |
E-mail:hongyangringdie@outlook.com
ପୋଷ୍ଟ ସମୟ: ନଭେମ୍ବର -15-2023 |